24+ A Process Is Said To Be Out Of Control When Information
A process is said to be out of control when. The control process contains special causes of variation. Control charts are used to determine whether a process is in statistical control or not. Whenever a value on a control chart is beyond the upper control limit UCL or lower control limit LCL the process is said to be out of control. A process is in statistical control when all special causes of variation have been removed and only common cause variation remains. When the process is out of control a higher proportion of the process lies outside of these specifications. D Process state is not dependent over this data. This implies that the output is not stable or predictable. Test 6 tells us If 4 out of 5 consecutive points lie on one side of the CL in the green band or beyond green band the. If you are looking at a chart pair X-bar and R X-bar and s or X and MR look at both charts. Control A process is said to be in control or stable if it is in statistical control. Your customer satisfaction line. C Data is not enough to predict.
Test 4 states that a process will be out of control if 14 consecutive points alternating up and down appear on the chart. If a process exhibits common cause variation it is said to be in a state of statistical control. The opposite conclusion gives the conditions for Type II error. A major objective of statistical process control is to quickly detect the occurrence of. A process is said to be out of control when It may also point to an intermittent problem. If the control chart fails to produce a signal when the process is actually out of control is _____ statistical process control _____ addresses the quality control of process of Jurans quality trilogy. Since so many out-of-control conditions are apparent in Figure 1 causal investigation would be occurring very frequently. If the Outputs are spread across outside the limits then the process is Unstable or Out of Control. If a process exhibits special cause variation it is said to be out of statistical control. The process with assignable causes is said out-of-control. One way to define out-of-control situations identified in Figure 262 is when the following occur. Different groups use different criteria to define when a process is out of control. The control process contains common causes of variation.
A process is said to be out of control when Type I error is described as the situation of the conclusion of the process state as out-of-control when it is in-control.
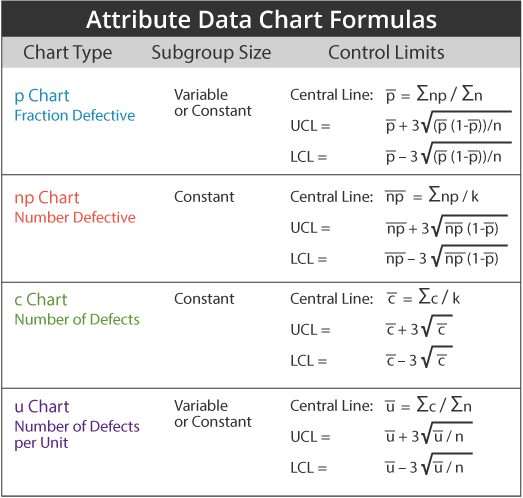
A process is said to be out of control when. A data point or points are above or below the upper or lower control limits respectively. Out-of-control occurrences are called special-cause conditions and can trigger a causal problem investigation. A process is said to be in the statistical control if it operates with _____ of variation.
Test 5 states that If 15 points in a row show up within the green bands on either side of the CL then the process is termed out of control. Type I error is actually concluding the process state being out-of-control when the process state is in-control. A process that is in control is affected only by common causes.
This just means that the process is working well without much noise. Points falling outside the control limits may be the result of a special cause that was corrected quickly either intentionally or unintentionally. As you stated a process is in control if it is between the UCL and LCL lines.
When the process is in control most of the production will fall between the lower and upper specification limits LSL and USL respectively. So for example people often feel out of control when. In other words if any measurement or test data is outside the control limits we will know that something wrong exists in the process.
This implies that the output is stable and predictable. The control process contains both common and special causes of variation. To meet customer satisfaction you need to check the process capability Process capability checks to see if the process meets some target value ie.
A process that is out of control is affected by special causes in addition to the common causes affecting the mean andor variance. When _____ is present the process is said to be out of control. Shifting of mean from the current value to a new value and remaining there is called _____ shift of the mean.
The outputs fall within the range UCL to LCL called process width then the process is said to be stable or in control. A True b False Answer. A process is said to be out-of-control if.
It is also an example of a CYCLE. If the process behaves consistently over time ie. In order to stop repressing material we must come to understand what and why we are repressing.
In this case some data points for the control charts will be out of the control limits. None of the above.
A process is said to be out of control when None of the above.
A process is said to be out of control when. In this case some data points for the control charts will be out of the control limits. In order to stop repressing material we must come to understand what and why we are repressing. If the process behaves consistently over time ie. It is also an example of a CYCLE. A process is said to be out-of-control if. A True b False Answer. The outputs fall within the range UCL to LCL called process width then the process is said to be stable or in control. Shifting of mean from the current value to a new value and remaining there is called _____ shift of the mean. When _____ is present the process is said to be out of control. A process that is out of control is affected by special causes in addition to the common causes affecting the mean andor variance. To meet customer satisfaction you need to check the process capability Process capability checks to see if the process meets some target value ie.
The control process contains both common and special causes of variation. This implies that the output is stable and predictable. A process is said to be out of control when In other words if any measurement or test data is outside the control limits we will know that something wrong exists in the process. So for example people often feel out of control when. When the process is in control most of the production will fall between the lower and upper specification limits LSL and USL respectively. As you stated a process is in control if it is between the UCL and LCL lines. Points falling outside the control limits may be the result of a special cause that was corrected quickly either intentionally or unintentionally. This just means that the process is working well without much noise. A process that is in control is affected only by common causes. Type I error is actually concluding the process state being out-of-control when the process state is in-control. Test 5 states that If 15 points in a row show up within the green bands on either side of the CL then the process is termed out of control.
An Introduction To Process Control Charts
A process is said to be in the statistical control if it operates with _____ of variation. Out-of-control occurrences are called special-cause conditions and can trigger a causal problem investigation. A data point or points are above or below the upper or lower control limits respectively. A process is said to be out of control when.